Aircraft with fuel-saving wing design flies first time – a project lead by SZTAKI
On the 19th of November 2019, an aircraft with aeroelastically tailored wings flew in real environment for the first time in the world. The wings carbon fibre composite orientation is changing by the wind’s direction. The flight of the craft that was developed under the SZTAKI-lead international project FLEXOP was to test ease passive damping of the load on the wings. SZTAKI has also responsible for building and functioning the board aviation (electric flight) system, including sensors and batteries inside the wings, and the autopilot system’s software and hardware components. With these, the craft is viable for repeatable experiments to collect data.
“The last four years hard work was crowned by gaining valuable data about the craft’s behaviour during test flights, thus proving our partners’ research results. Thanks to the extraordinary work of the board data collecting system built by SZTAKI, we can also easily document our results achieved during the project as well” – said Bálint Vanek, head of SZTAKI’s Aerospace Guidance, Navigation, and Control Group
20 minutes of flying = 10 gigabyte of data
The experimental aircraft flew several times before but was remotely controlled by its operators through radio signal. This time however the autopilot was activated which is important from the perspective of scientific research: it can recreate special experimental manoeuvres with much more accuracy compared to manual control. This is important to compare traditional composite wings with the project’s lighter yet more flexible ones.
Due to the carbon fibre’s specially oriented and tailored design, wind may be as powerful from the optimal direction as its needed to spare mass, thus new generation wings may result a more economical and sustainable flight while doing the same manoeuvres as traditional aircraft do.
Since the craft weights 65 kilograms and has a 7-metre wingspan, regulations are stricter than the case of a drone that merely weights 25 kilograms. Flights required to answer questions arising research are planned and accurately designed in advance. Manoeuvres and routs are being exerted in simulation by the team of Munich’s university of technology (Technische Universität München). They fly the craft in real environment as well.
The first real flight took place at the Oberpfaffenhofen airfield next to Munich on a regular day with commercial traffic. Because of this, the experimental craft’s ground control HQ is not just communicating with the two operators involved, but also with the airfield’s tower. The manoeuvres are implemented by the craft’s operator according to orders by the flight test operator through headphones. Meanwhile, the second operator is closely following every movement to have a chance of intervention in case of emergency.
Airspace for experimental flights is strictly bounded (2x05 kilometres), so ground control is helping the operator to keep the craft within borders. The board system engineer is monitoring device behaviour and data in real time: during a short 20-minute-long flight, 8-10 gigabytes of flight data is collected. Research partners analyse these results to confirm their own and to make the mathematical model of the craft even more accurate.
Airbus is also a member of the project, meaning these results may eventually find their way to commercial aviation.
🇪🇺 This project has received funding from the European Union’s Horizon 2020 research and innovation programme under grant agreement No 636307
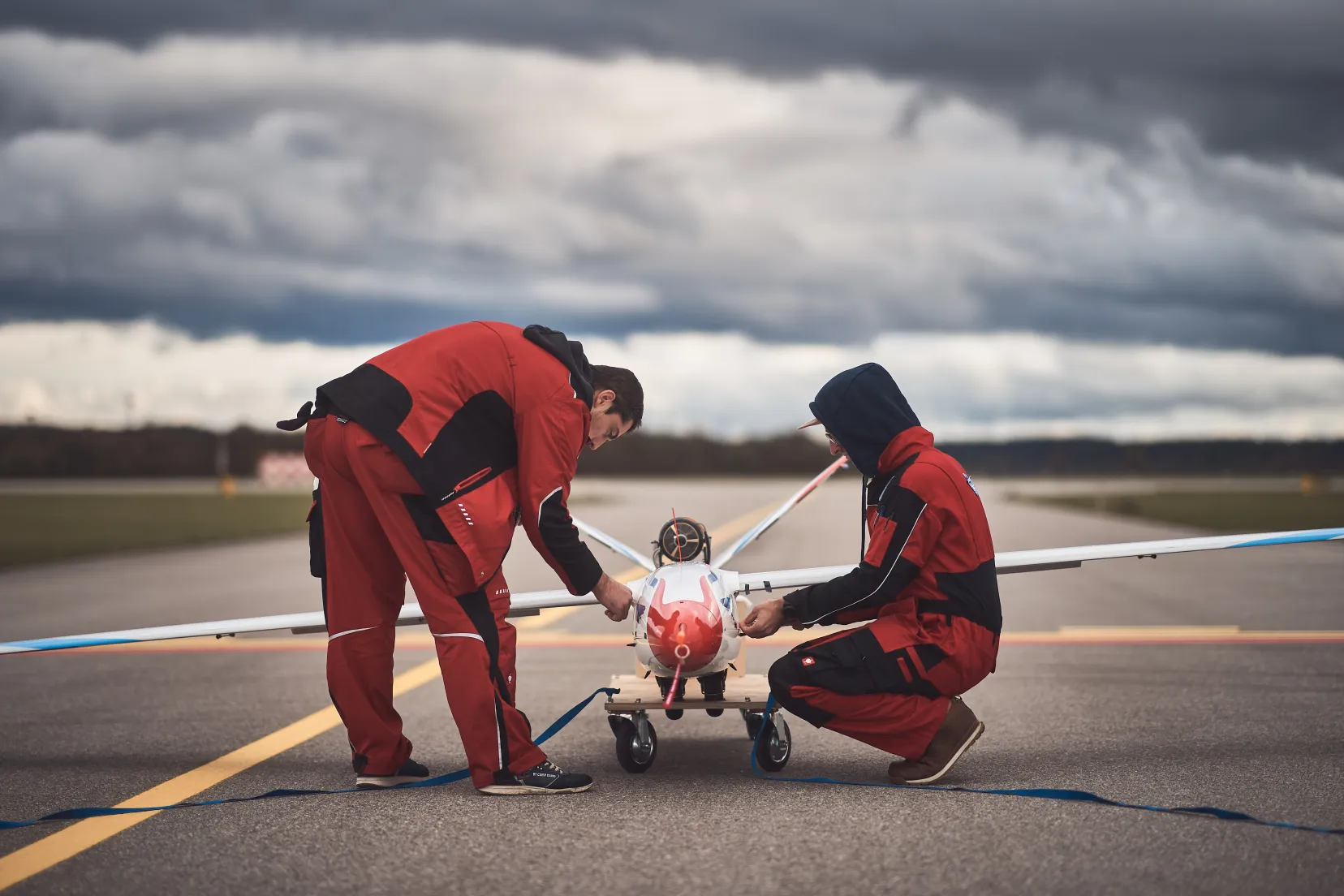